HSE Risk management software
Optimize safety, ocuppational health and environmental management with ZYGHT. Our SaaS software offers advanced solutions to manage risk, comply with regulations and improve your company’s operational efficiency.
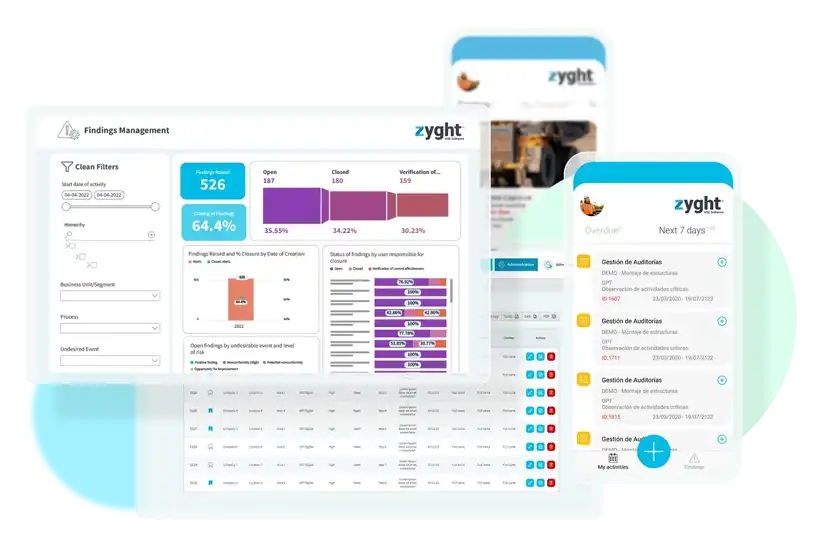
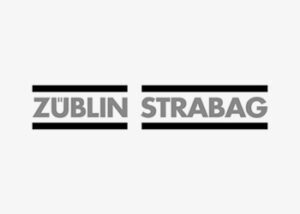
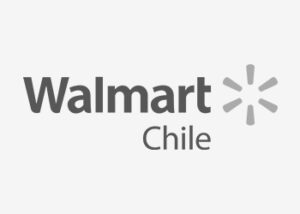
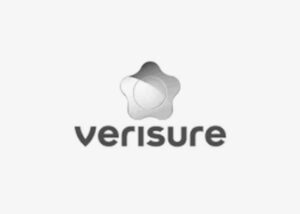
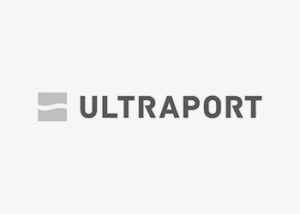
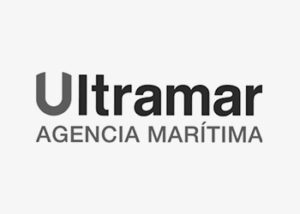
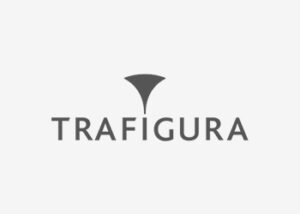
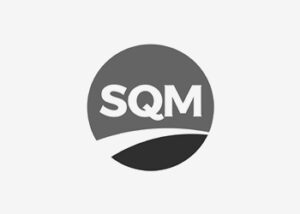
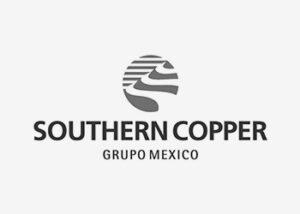
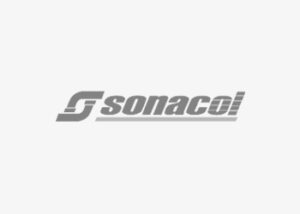
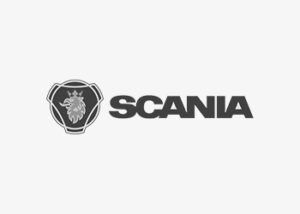
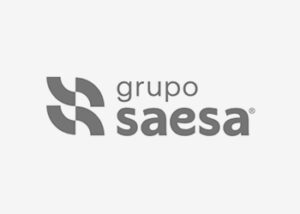
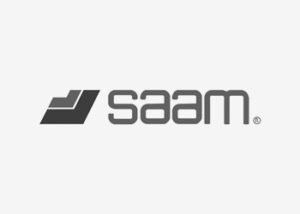
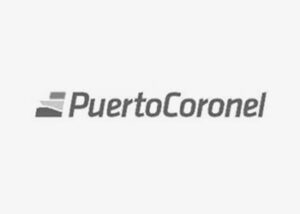
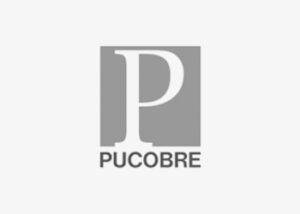
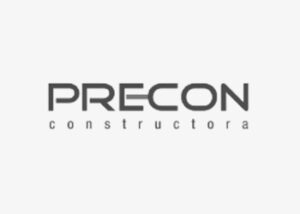
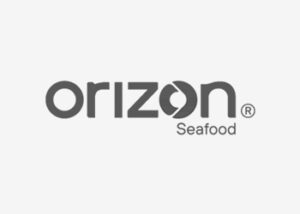
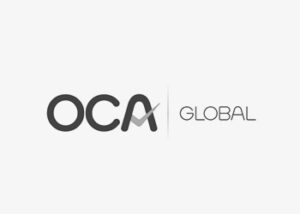
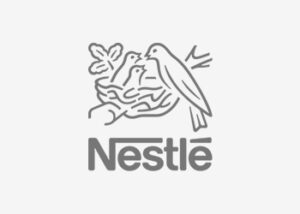

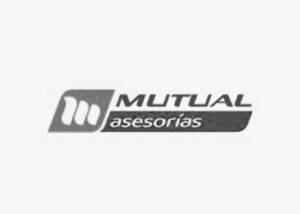
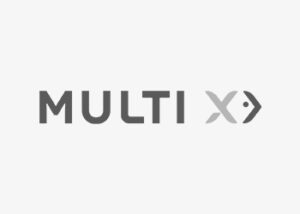
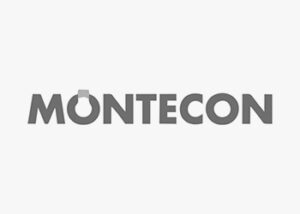
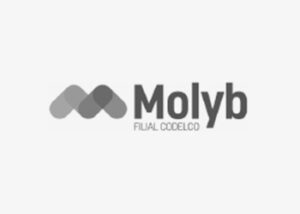
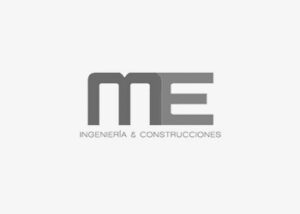
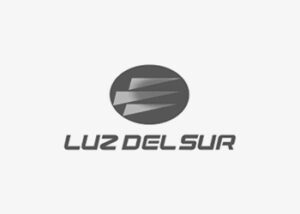
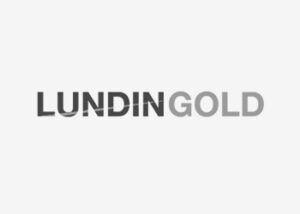
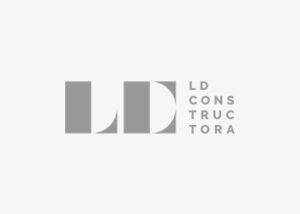
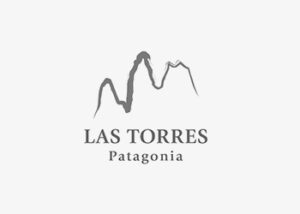
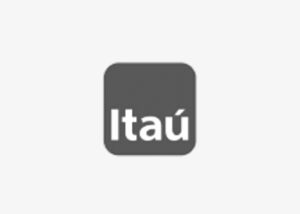
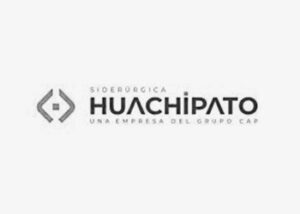
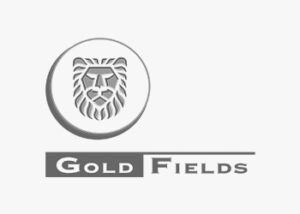
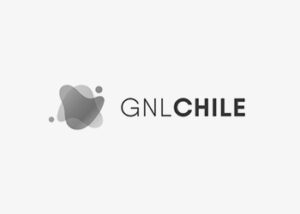
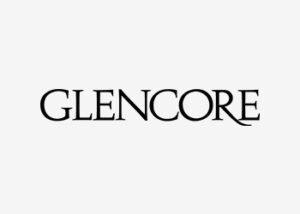
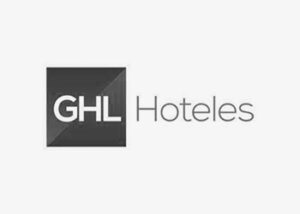
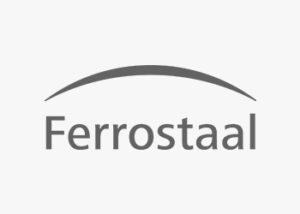
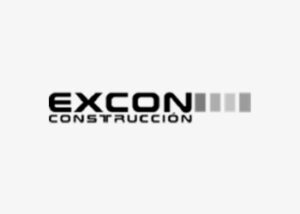
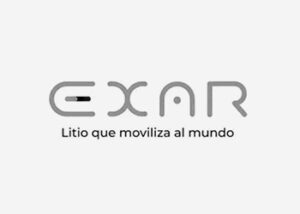
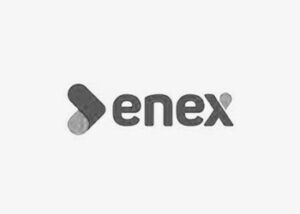
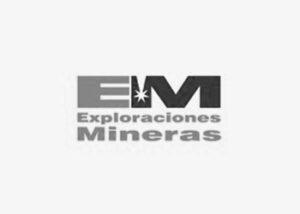
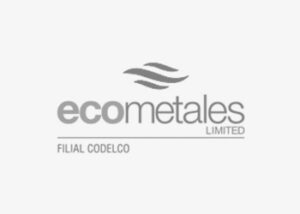
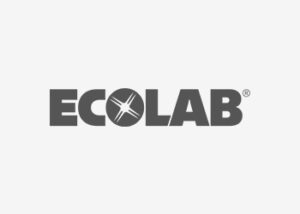
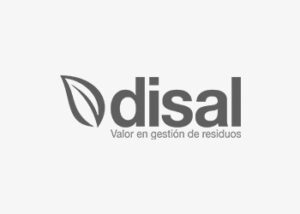
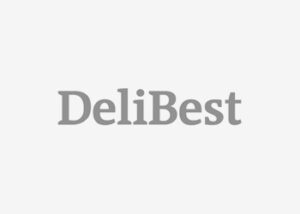
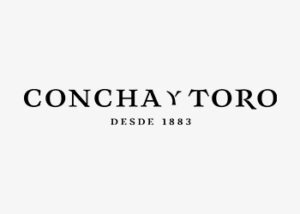
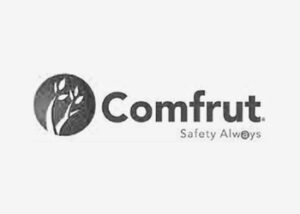
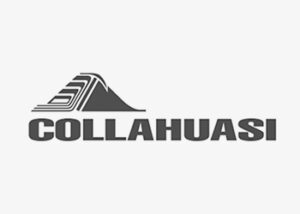
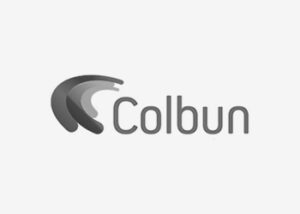
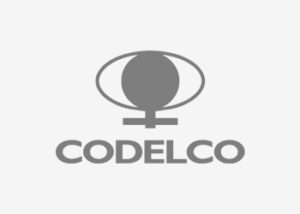
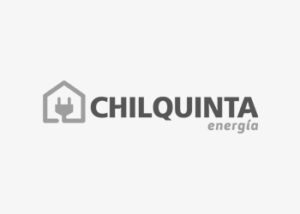
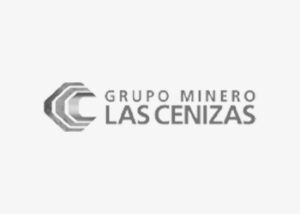
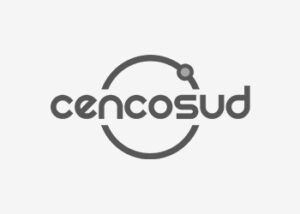
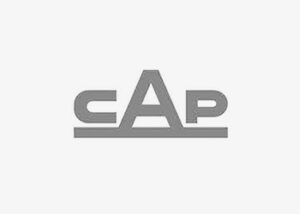
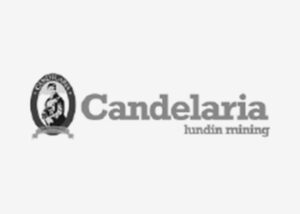
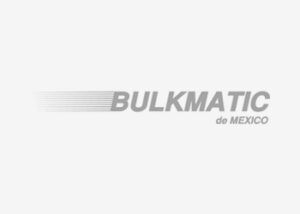
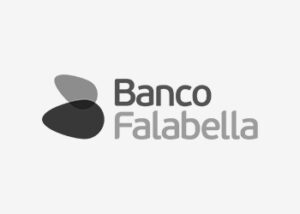

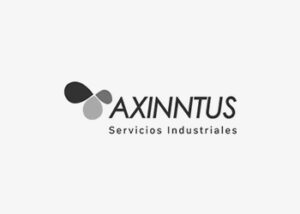
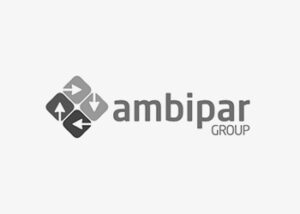

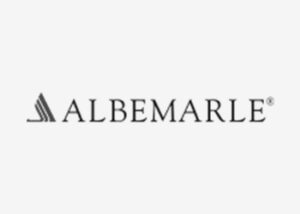
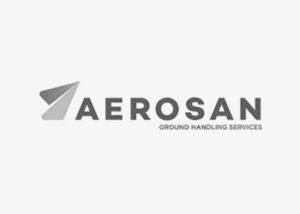
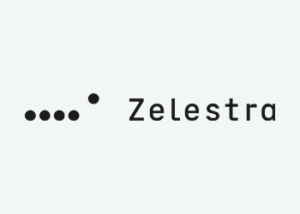
Occupational health, safety,
and environmental management
in a single software
Streamline and digitize your safety at work and occupational health processes
ZYGHT is the premier Software as a Service (SaaS) for occupational health, safety at work, and environmental management. With over a decade of experience in aiding companies to achieve OSHA compliance, and optimize their processes, ZYGHT serves as an integrated HSE Risk Management Software that leverages cloud-based information, mobile applications, and data analytics, offering the flexibility to integrate and customize through its various modules.
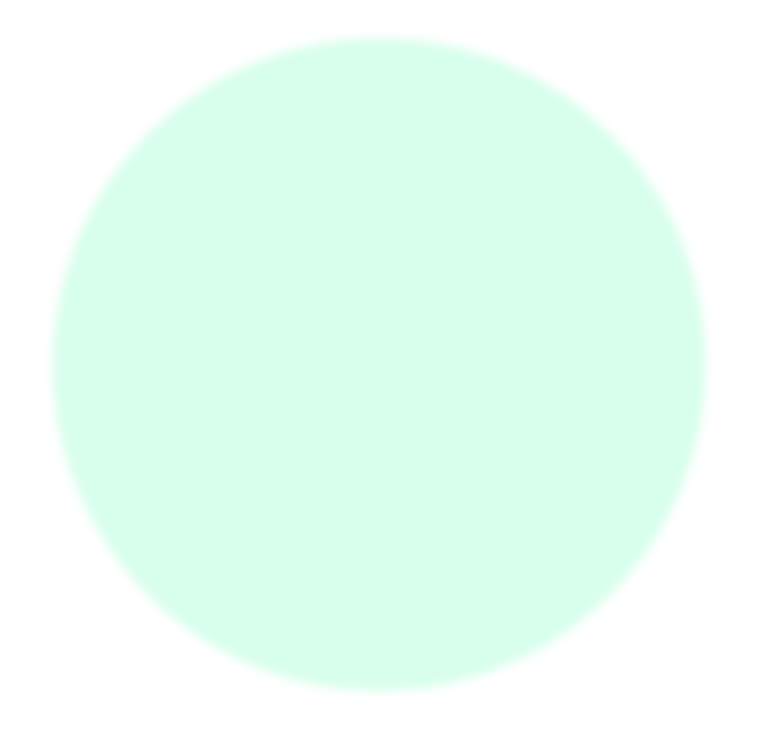
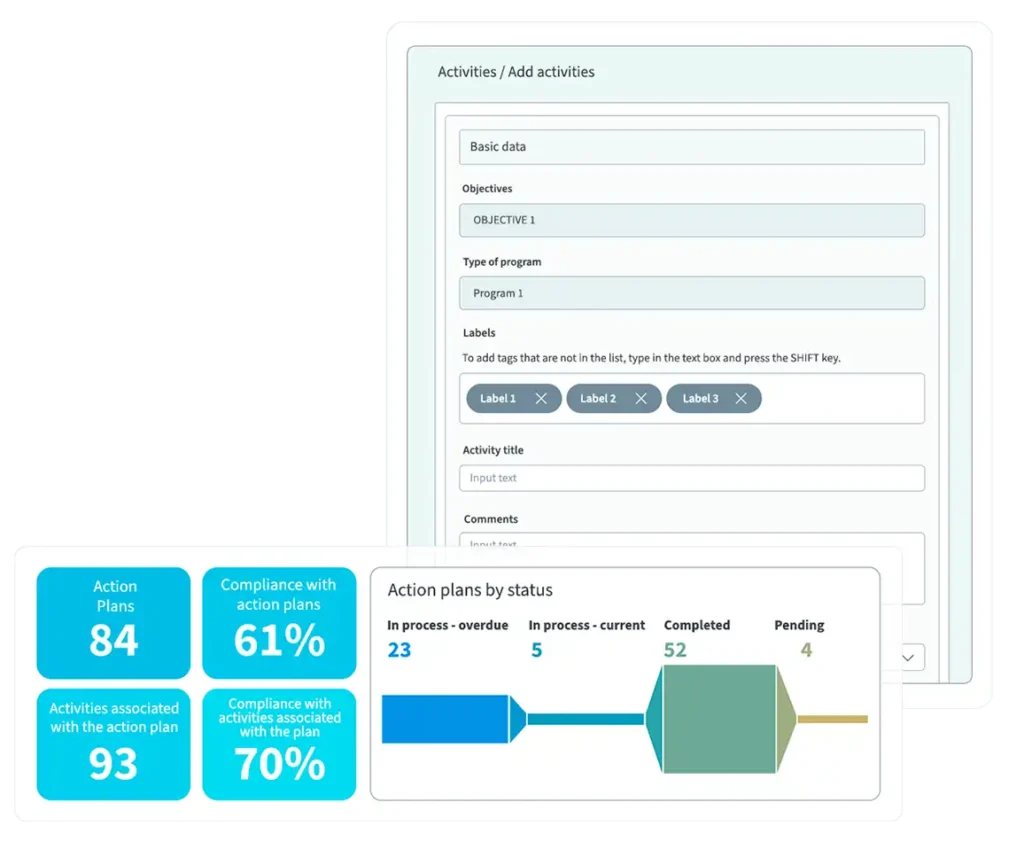
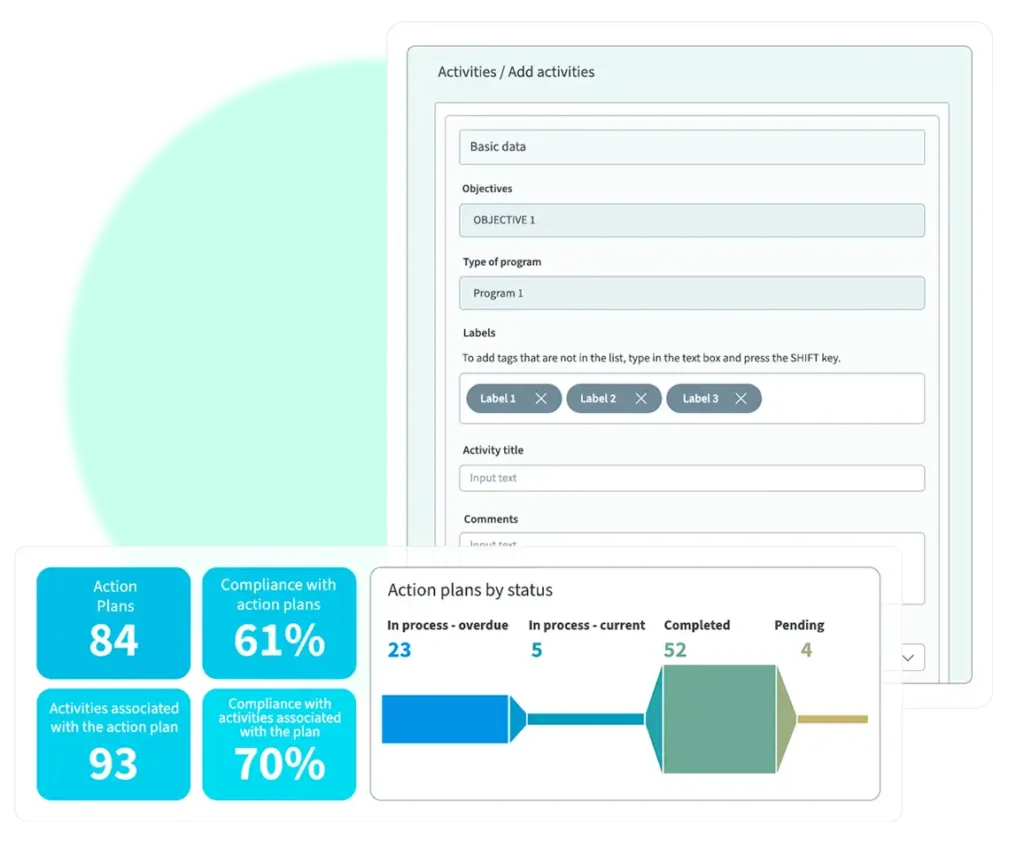
In need of OSHA compliance?
Our software aligns seamlessly with the highest international OHS and sustainability standards and regulations, enhancing and promoting adherence to ISO 45001, ISO 14001, and ISO 9001, and bolstering commitment to HSE and ESG practices.
Minimize your
risk and analysis time
ZYGHT is a risk management software that facilitates data visualization and reporting, refining your HSE processes for risk reduction and improved decision-making.
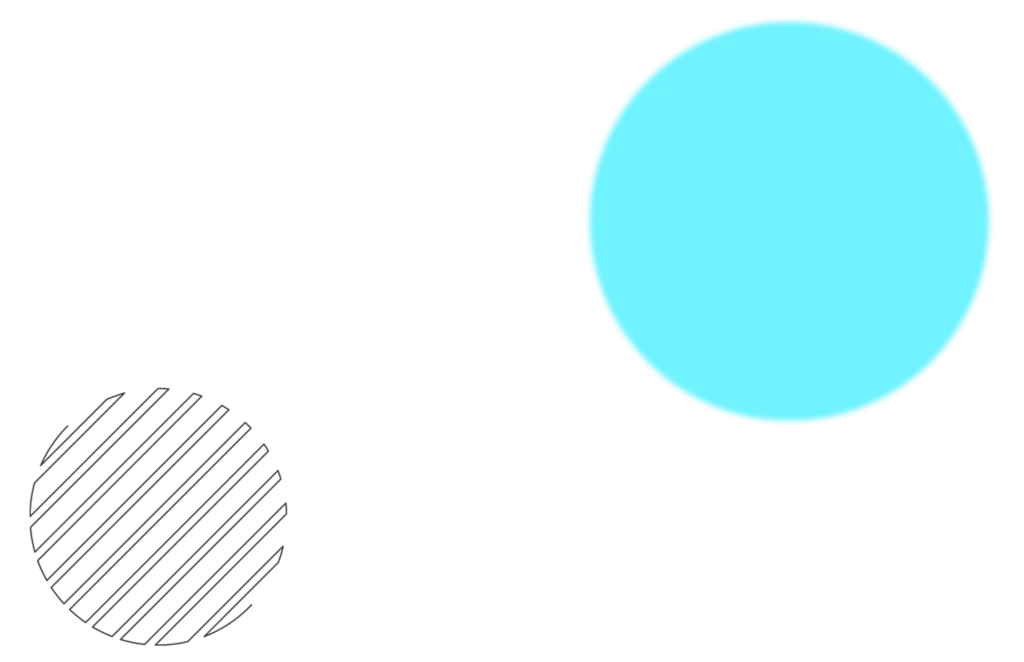
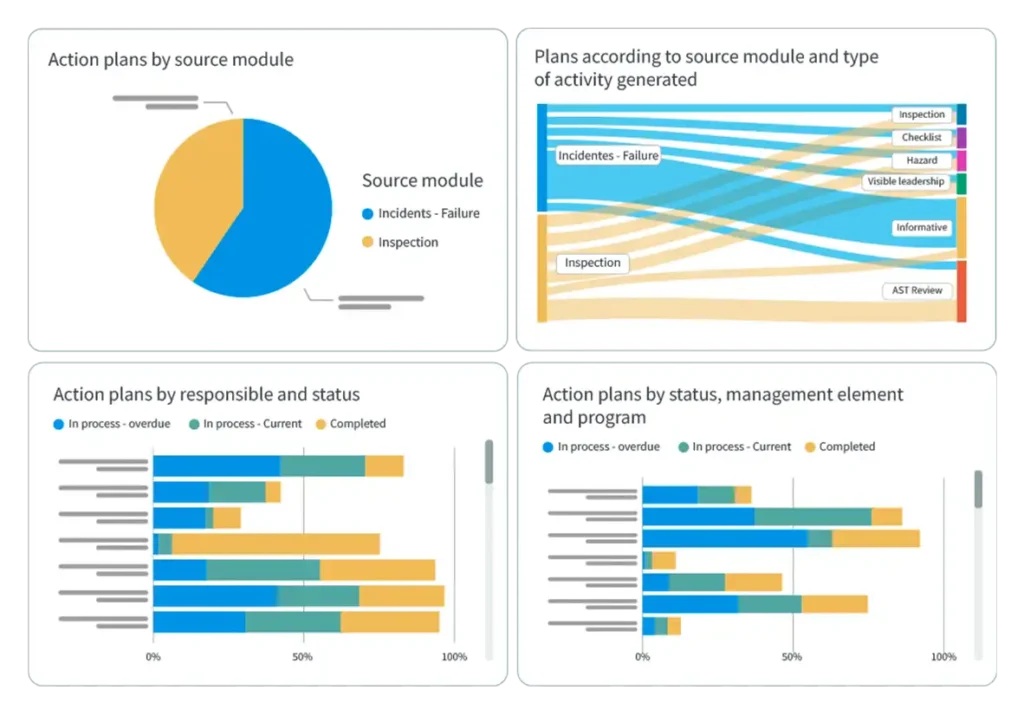
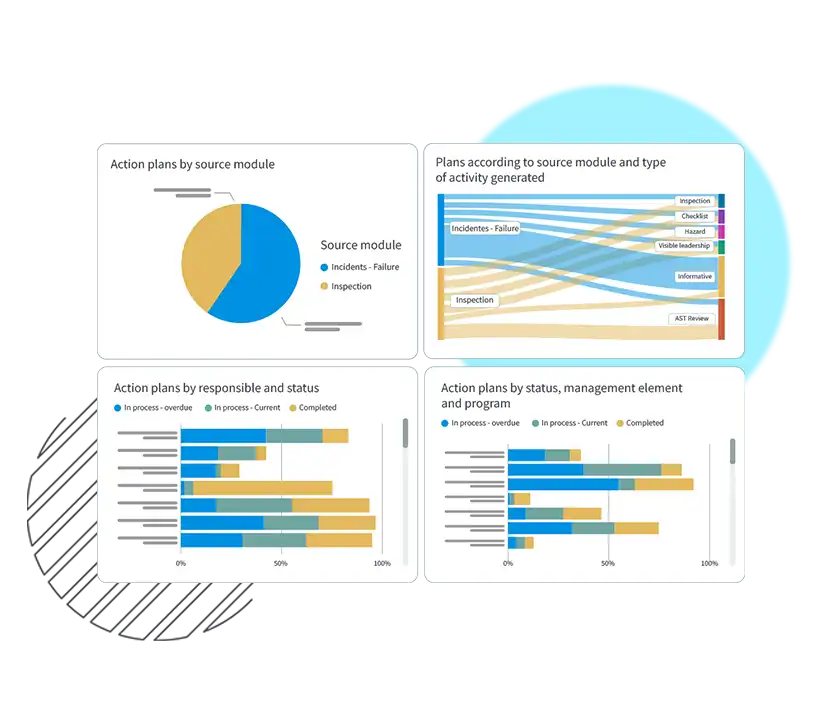
Leading companies across various industries trust ZYGHT
Leading companies across various industries trust ZYGHT
Discover why ZYGHT is the leading software in safety at work, occupational health, and environmental management.
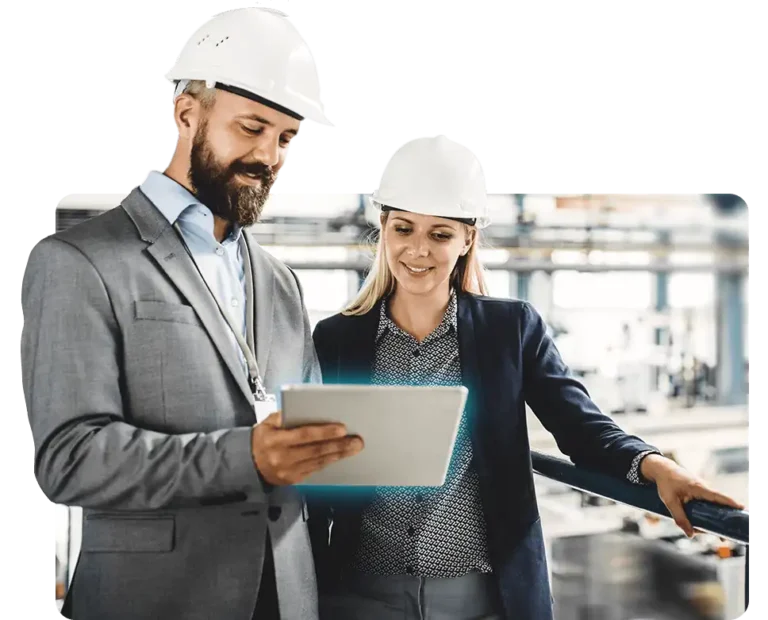
ZYGHT has enabled us to save 75% of the paper used by the SSO area and reduce the fatality rate by 30%.
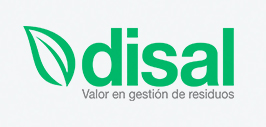
Romina López
DISAL deputy safety manager
Success Stories
For more than 10 years, ZYGHT has been transforming risk management in large companies in various industries through its HSE solutions.
We are part of a worldwide network
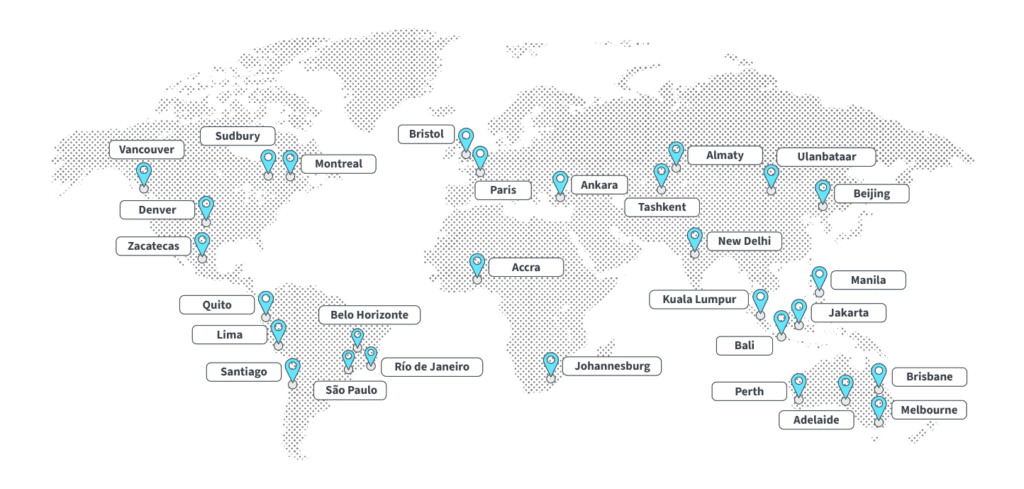
- Unique combination of long-term investment and operational independence.
- Experience in environmental and social governance best practices.
- Worldwide network with first-class support.
Try our software today
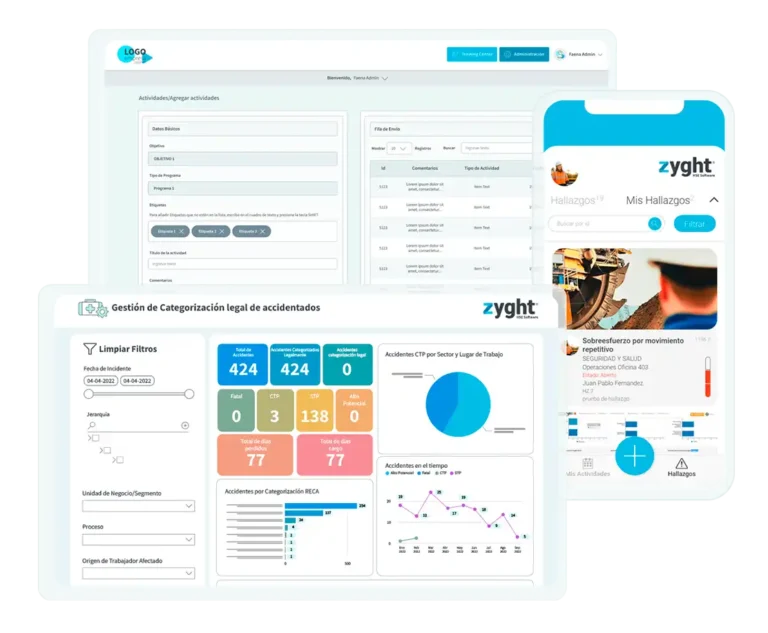
ZYGHT comprises a series of modules that provide solutions to risk management and operational controls for compliance with protocols and regulations governing business sustainability and social license to operate.
Leave us your details in the form and one of our executives will contact you shortly.